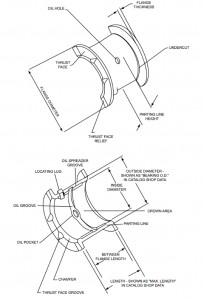
Engine bearings have to withstand punishing loads in today’s engines. Smaller displacements, turbocharging and higher horsepower ratings mean crankshaft and connecting rod bearings are being subjected to heavier loads. This has led to the development of some new bearing alloys and coatings that enable these parts to survive.
It’s the same story with high performance. Today’s hi-flow, aftermarket, CNC-ported cylinder heads, high lift killer cams and induction system power adders (blowers, turbos and nitrous) are making more power than ever before, and really hammering the bottom end of the engine. If the bearings can’t take it, the engine won’t last.
The stock production aluminum bearings that are used in many late model engines can usually handle up to 500 horsepower before they get into trouble, and over 300 horsepower in a turbocharged four-cylinder engine. But once you get beyond these power levels, bearing fatigue can be a problem. At that point, you have to upgrade to a stronger material of some type, be it a tougher aluminum alloy or a performance tri-metal bearing.
The rod bearings take the most punishment because of the reciprocating motion of the pistons and rods. The load on the rod bearings change with the crank angle and RPM, and whether the cylinder is on its power stroke, compression stroke, intake stroke or exhaust stroke. The upper rod bearings bear the heaviest loads during the power stroke when combustion pressure is ramming the piston and rod down hard against the crank. But the upper rod bearings can also see heavy loads in boosted engines during the compression stroke, and on the exhaust stroke, too – especially in engines that are burning nitrous or nitro. The lower rod bearing can also experience extreme G-forces and loading in a high-revving engine during the exhaust stroke. That’s when most connecting rod and rod bearing failures occur.
The bearings in a stock engine typically had to withstand loads of up to 6,000 PSI or higher depending on the engine’s power output per cubic inch. In a performance engine or a high compression diesel, peak loads can range from 8,500 up to 10,000 PSI or higher.
Bearing manufacturers offer a range of materials with various strength and fatigue resistance ratings to handle every kind of engine application, stock or performance. Some of the better aluminum bimetal alloys (aluminum overlay on a steel shell) can safely handle peak loads of up to 8,000 PSI or higher, while many “race series” tri-metal bearings are good for 10,000 PSI or more. Some specialty bearing materials such as those that have been developed for big, heavy-duty, high output, turbo diesel engines are rated as high as 20,000 PSI. Some of the more exotic bearing materials are applied to the bearing shell using “sputter” or a “PVD” (physical vapor deposition) process in a vacuum-controlled environment. This allows the material to be built up to the desired thickness with a high degree of accuracy.
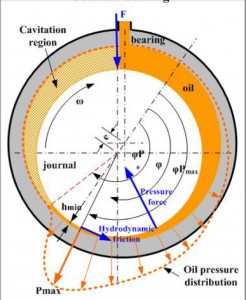
Alloys And Attitudes
The ideal bearing provides a good combination of durability, fatigue resistance and embedability. Durability means the bearing is strong enough to withstand the peak loads it experiences inside the engine. Fatigue resistance means the bearing won’t crack or flake after millions of engine revolutions and combustion cycles. Embedability means any dirt or wear particles that find their way into the oil film between the bearing surface and crank journal will be pressed into the bearing surface rather than scoring the crank journal.
Engineers today have software that can simulate the loading on a bearing based on an engine’s displacement, bore and stroke, horsepower output, compression ratio and RPM. They can predict how well a given bearing material will hold up in a particular application. So using their software and real world experience, they can recommend a specific type of bearing based on what your requirements are. Are you building a stock motor? A street/strip dual-purpose engine? A petal-to-the-metal drag motor, or truck or tractor puller engine? A circle track or endurance motor? A marine inboard motor?
For most racing applications, you want a bearing that is both durable and fatigue resistant. Drag racing can be really hard on bearings because a relatively cold engine suddenly goes from idle to full throttle for maybe 4 to 12 seconds until the car reaches the end of the strip. The short burst, extreme loading of the bearings means the bearings have to be the right material to withstand the hammering. That’s why tri-metal bearings have traditionally been used in drag motors. But high strength aluminum bearings can also take this kind of short-term abuse, too, according to the manufacturers who make them. In fact, one crankshaft supplier we talked to for another article indicated that aluminum race bearings hold up better in a blown motor than tri-metal bearings.
With a dirt track motor, the engine is going to run a series of laps, alternating between wide open throttle and throttle off. The bearings experience peak loading for a longer period of time when the driver floors the throttle out of the turns. And a feature event usually goes at least 25 or more laps, so durability and fatigue resistance are critical. Tri-metal bearings have traditionally been the bearing of choice for this type of racing. But aluminum performance bearings are also being used in some of these engines.
In a marine application, fatigue resistance is even more important because the engine usually runs flat out for long periods of time. Tri-metal is probably the most common choice here, too.
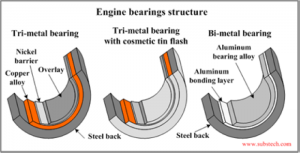
Bearing Construction
Tri-metal bearings are made of a copper-lead-tin alloy applied to a steel shell with a thin lead babbit overlay. The babbit overlay provides good seizure resistance. Reducing the thickness of the babbit overlay to .0005 inches is one of the tricks bearing engineers can use to increase fatigue resistance in a performance bearing. A thinner overlay still provides a good bearing surface, but much less embedability. Some tri-metal bearings may also have a hardened surface layer, which improves the load carrying capacity of the bearing.
Aluminum alloy bimetal bearings have been the bearing material of choice for stock production engines because they are long-lived. Aluminum bearings typically have an aluminum-tin-silicon alloy overlay about .012 inches thick on a steel shell. Aluminum alloys can be both strong and soft, providing good strength and embedability. Tin (which may be 6 to 20 percent of the alloy) reduces friction and acts as a solid lubricant. Hard particles of silicon (maybe 2 to 4 percent) may also be added to improve strength and wear resistance. Silicon is essential for engines with cast iron crankshafts to reduce the risk of seizure if the oil film is disrupted. Small amounts of copper, nickel and other elements may also be added to the aluminum alloy to further enhance the properties of the bearing material.
Lubrication Issues
Bearing lubrication is critical from the instant the engine turns over until it is shut down. If a rod or main bearing is starved for oil causing the oil film between the bearing surface and crank journal surface to go away, galling, seizure and failure can occur in an instant.
The babbit top layer on a tri-metal bearing serves as a sacrificial layer when this happens. It can prevent seizure until the babbit wears away. At that point, the situation goes south very rapidly. The bearing usually seizes, locking up the motor or breaking the connecting rod.
With aluminum bimetal bearings, the situation is somewhat different according to tests conducted by one bearing manufacturer. If the oil film between the bearing and crank goes away, there is actually less risk of seizure and failure with their performance bimetal aluminum racing bearing.
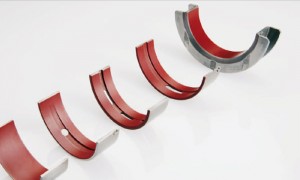
Coated Bearings
One way engine builders have tried to reduce the danger of engine damage if an engine loses oil pressure during a race is to use coated bearings when they put the engine together. Aftermarket coating suppliers have offered various proprietary coating materials for bearings, pistons and other parts for many years. Only recently have coated bearings become mainstream and readily available from major bearing suppliers. Some bearing suppliers coat their own bearings while others still use an outside vendor to apply the coatings.
Bearing coatings can provide several benefits. They can prevent dry-starts to extend bearing life, as well as provide some degree of protection and seizure resistance if the engine loses oil pressure in a race. Some coatings also have oil retaining properties that help maintain an oil film between the bearing and crank journal. A coating also improves conformability to the crankshaft journal, as well as embedability.
A dry film polymer-based coating will sacrifice itself if the engine loses oil pressure – which can often make the difference between a ruined crankshaft and blown motor or a motor that can be easily rebuilt and raced again with a new set of bearings.
Some bearing coatings contain PTFE (Teflon) because of its anti-friction characteristics. The polymer resin may also contain other ingredients such as graphite, molybdenum disulfide for added lubricity, and/or microscopic iron particles to improve wear resistance and durability. One manufacturer who applies a special iron-based dry film coating to its engine bearings claims its coating reduces wear 500 percent over an uncoated bearing, and improves fatigue resistance 20 percent.
Coating bearings are even being used in some late model production engines. Some OEMs are now using polyamide coated bearings in engines with idle Stop/Start systems as well as some light truck diesel engines. One bearing supplier reported that it will introduce a new aftermarket coated bearing for the Ford 6.7L Powerstroke diesel in early 2016. Other applications will likely follow.
As for the Start/Stop applications, shutting the engine off when a vehicle stops moving and remains motionless for more than a few seconds improves the vehicle’s overall fuel economy, especially in city stop-and-go driving. But it also means the bearings in these engines experience more cranking cycles and an increased risk of metal-to-metal contact between the bearings and crank. Lubrication is minimal until the rotation of the crankshaft forms a hydrodynamic oil wedge between the bearings and crank journals. Uncoated bearings typically show severe wear after 100,000 start cycles, whereas coated bearings that are designed for 250,000 to 300,000 starts show almost no measurable wear.
The new polyamide coating that is being used in these applications has an added benefit: it also improves the durability of aluminum bearings to that of many tri-metal bearings. The amide-coated bearings can handle peak loads that are up to 25 percent higher than uncoated aluminum bearings made with the same alloy. The amide coating also cuts the coefficient of friction in half compared to a bare aluminum uncoated bearing.
The new high tech bearing coatings are unaffected by the type of fuel used (standard gasoline or E85) or the type of oil (conventional or synthetic). The coating also allows the use of lower viscosity motor oils for added friction reduction and fuel savings.
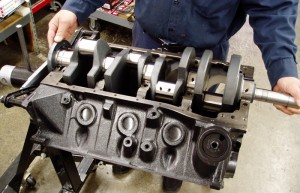
Bearing Loads And Friction
Years ago, NASCAR engine builders discovered that if they ran crankshafts with smaller diameter journals, they could pickup some extra horsepower. Reducing the circumference of the bearings reduced friction. A crankshaft with smaller journals was also lighter and revved faster. But there were a couple of tradeoffs. The smaller journals also reduced the strength of the crank, so there was a limit as to how far they could go without dangerously weakening the crank. Also, reducing the diameter of the journals increased the loading on the bearings.
The larger the bearing, the broader the area over which the load is distributed. The smaller the bearing, the more concentrated the load is over a given portion of the bearing. Tightening up the bearing clearances and using lower viscosity oil helps distribute the load over a broader area of the bearing.
Regardless what type of bearings are used in an engine, clearances have to be precise and correct for the oil viscosity that will be used to lubricate the motor. Thin, low viscosity motor oils require tighter bearing clearances than heavier viscosity racing oils such as 20W-50 or straight 40, 50 or 60 weight oils.
Here are some recommended rod bearing oil clearances for various oil viscosities:
.0015 to .0018 for 5W-20 or 20W
.002 to .0024 for 5W-30 or 30W
.0025 to .0029 for 10W-40 or 40W
.0030 to .004 for 20W-50 or 50W
.0041 to .005 for 10W-60 or 60W
For main bearings:
.0015 to .002 for 5W-20 or 20W
.002 to .0025 for 5W-30 or 30W
.0026 to .003 for 10W-40 or 40W
.0031 to .0041 for 20W-50 or 50W
.0042 to .0052 for 10W-60 or 60W
Tighter bearing clearances reduce noise and vibration in an engine, but also require more precise and accurate machining. If you can’t achieve good main bore geometry (less than .002˝), you shouldn’t try to run tight clearances.
Also, if you’re building an engine with aluminum rods, the rods will undergo more thermal expansion when they get hot than steel rods, so you have to compensate for that when setting up your bearing clearances.
The type of racing will also affect rod and main bore distortion as well. Drag racing and truck/tractor pulling can create more bore distortion than other types of racing, so again you may have to compensate when setting up the bearing clearances.
The best way to check bearing clearances is with a dial bore gauge and micrometer rather than a plastic strip. Measure the diameter of the crank journals, then measure the inside diameter of the rod bearings when they are assembled in the rods, and the main bearings when they are assembled in the main bores. Write all the numbers down, then subtract to determine the bearing clearances.
Bearings should never be installed dry. Lubricate with engine oil or assembly lube, make sure all oil holes are properly aligned and that there are no dirty fingerprints or contaminants on or behind the bearings.
Finally, if a crank won’t spin freely in the block when the main caps have been tightened down, recheck the clearances because one or more bearings are too tight, or there is a misalignment problem in the main bores, or the crank is bent.