Back in the early ’90s, when Chrysler realized that it would need a new truck motor to replace its 318/360 Magnum engines to meet the coming emissions standards, the company considered two pushrod engines along with one SOHC design and concluded that a pushrod motor with a pair of Hemi heads that really breathed would make a great truck engine and could still be used in its cars.
This is how the 5.7L Gen III Hemi was born in 2003. Although the chamber had small “squish shelves” on both sides, the heads did have Hemi-shaped chambers that enabled them to incorporate big valves and generous ports that actually outflowed the Chevy LS1 heads by 24% at 0.500” lift, so the new motor delivered 345 hp and 375 lbs. of torque. That’s 41% more horsepower and 12% more torque than its 360 Magnum, so it was well received in the market and recognized as one of the ‘10 Best Engines’ by Wards magazine for five years in a row.
Chrysler included provisions for a “multiple displacement system” (MDS) in the original design, so the main oil galleries were used to supply oil directly to the solenoids that disabled the lifters and the oil for the lifters came down through the pushrods from the rockers up topside.
That’s probably why the MDS system has been so successful and trouble-free in these engines, but the original block wasn’t designed to include the variable valve timing (VVT) that was the next step up in technology, so Chrysler had to redesign the block in order to update the engine in ’09.
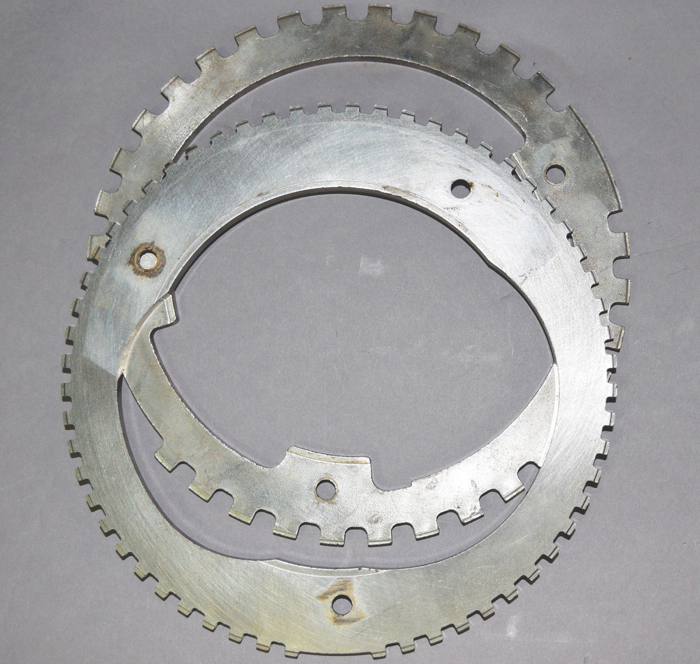
That’s where it all started, but by the time they were done, the rocker assemblies were about the only two things that were carried over from the original engine. Chrysler made some major changes to the block and heads, but there were a bunch of evolutionary upgrades, too, including bigger valves and ports, updated cams and lifters along with a stronger crank and rods and a high volume oil pump. With that in mind, let’s take a look at what’s new and different.
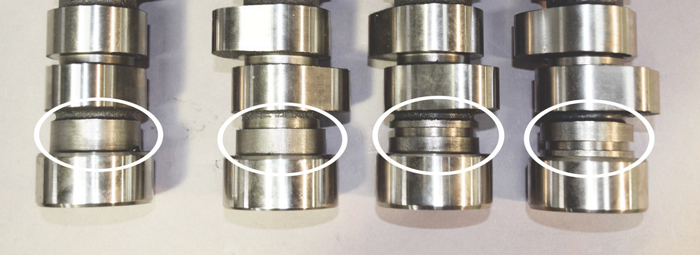
BLOCK
Adding VVT to the Hemi engine required a new block that had three additional oil passages and an extended front cam bearing that allowed them to supply oil to the cam phaser through the front journal. The front of the block above the mains was moved out by about 0.600” so it ended up flush with the side rails on the timing cover. This change allowed them to add an oil passage that connected the main oil gallery to the oil control valve that directed oil to the phaser through the front cam journal. The cam bore for the front journal was increased by about 0.180” and it was about 0.550” longer, too.
There were two other small changes made to the block; the hole for the temp sender on the left side of the timing cover was removed and one more bolt boss was added on the driver’s side, close to the front and about midway up on the block. The new block was a 53021319DK casting.
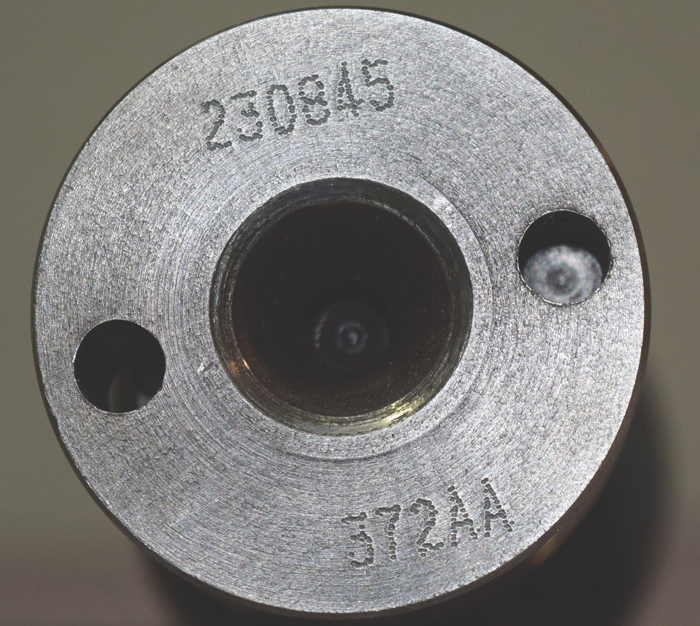
CRANK
The VVT motors came with a new crank that’s a 53021300BB casting. It’s still made of cast nodular iron, but it’s considerably stronger than the original design, according to Chrysler. The most noticeable difference is the length of the tapered area in front of the main journal that creates the step that locates the crank gear on the snout. It was extended by about 0.460” so the crank gear would line up with the cam gear that was moved forward when the block was modified for VVT.
RODS
The powdered metal, forged rods were supposedly redesigned to make them stronger, but they look just like the early ones except for a slight difference in the balance pad on the big end. However, we tend to believe that they’re stronger because the VVT motors make more horsepower and torque and the original rods were the weak link in the Gen III motors, so they were definitely due for an upgrade. We wouldn’t recommend using the early rods in the late motors.
All of the VVT motors were supposed to have had bushed rods according to an early press release and it appears that a few of the early ’09 Durangos actually came with bushed rods, but all of the engines built since then have had press fit pins.
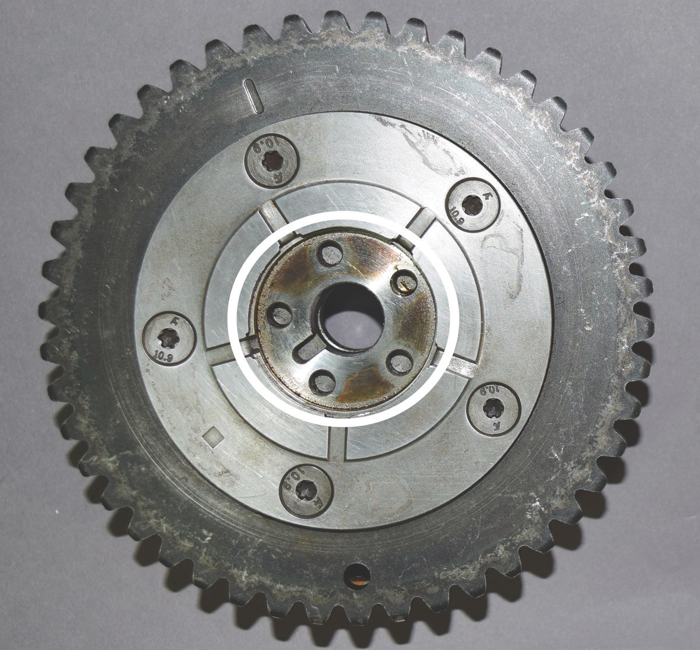
PISTONS
The original Gen III piston was modified to accommodate a new, narrow ring pack that had 1.20/1.20/2.0mm rings instead of the 1.50/1.50/3.0mm rings that were used up through 2008. Other than that, it appears to be the exact same piston that even has the same identification numbers on the inside of the skirts.
CAMS
This is where it gets interesting, because there are five applications that all share VIN code “T” even though they’re all different and they actually use five different cams that are NOT interchangeable. The cams for the MDS motors are unique because four of the intake lobes have a “primary ramp” that takes up the “locking lash” in the MDS lifter before the “secondary ramp” closes the check ball in the lifter, and the timing on the four MDS exhaust lobes was advanced by a few degrees.
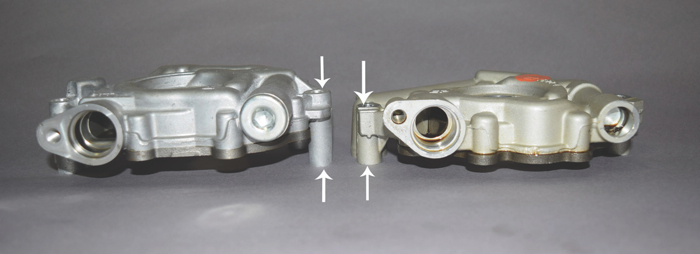
The bottom line is that these cams can’t be interchanged because each one is unique to a particular application so it won’t work in any other engine. We bought four of the five cams – we couldn’t get the one that was used in the hybrids – so we could identify them by vehicle application along with the part number that’s etched on the back of the rear journal and the ID grooves that are machined in the barrel that’s in front of the back journal.
Chrysler originally said that the VVT cams would be made of “high strength billet steel,” but our samples are all cast iron, so apparently they made a running change. Here’s the list of the cams:

1.
The Challenger with a manual transmission uses a p/n 53022064BD that has one groove machined in the barrel, tight against the rear journal, along with 064BD on the back side of it. It’s a performance grind that has VVT, but it doesn’t have MDS because that requires a torque convertor that can be momentarily unlocked to absorb the torque spike that occurs when the four disabled cylinders are reactivated.
2.
The 2500 and 3500 trucks use p/n 53022314AD that has one groove machined in the middle of the barrel that’s in front of the rear journal and 314AD stamped on the back of it. It’s a truck cam that has VVT, but it doesn’t have MDS because the ¾ ton and 1 ton trucks aren’t required to meet the federal CAFE fuel economy standards like the ½ ton trucks, so fuel economy isn’t an issue.
3.
All of the 1500 pickups came with a p/n 53022263AF cam that has 263AF on the back of the journal, but there isn’t a groove in the barrel. This cam was also used for the ’09-’10 Aspen and Durango, except for the hybrids. It includes VVT, MDS and SRV – the short runner valve – for the active intake, so it has a very sophisticated profile.
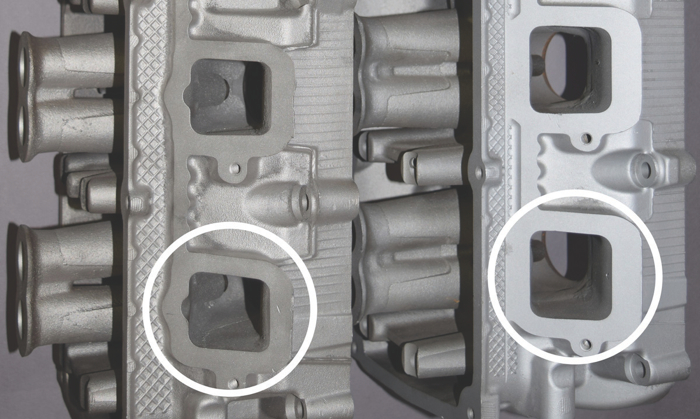
4.
The fourth cam fits all the cars and Jeeps with automatic transmissions along with the new Durango that was based on the Grand Cherokee platform starting in 2011. It’s a p/n 53022372AA that has one groove machined all the way forward on the barrel in front of the journal and 372AA stamped on the back of the journal. This one has VVT and MDS.
5.
The last one is for the Aspen and Durango hybrids that were built in limited numbers in 2009. It’s supposed to be a p/n 53022065BE, but it came up as a discontinued number when we ordered it, so all we know is that it probably has 065BE stamped on the back of the rear journal. According to one of the articles we found on these vehicles, the hybrid engines came with “a modified version of the cam for a passive intake with MDS,” but it’s definitely not the same as any of the other cams.
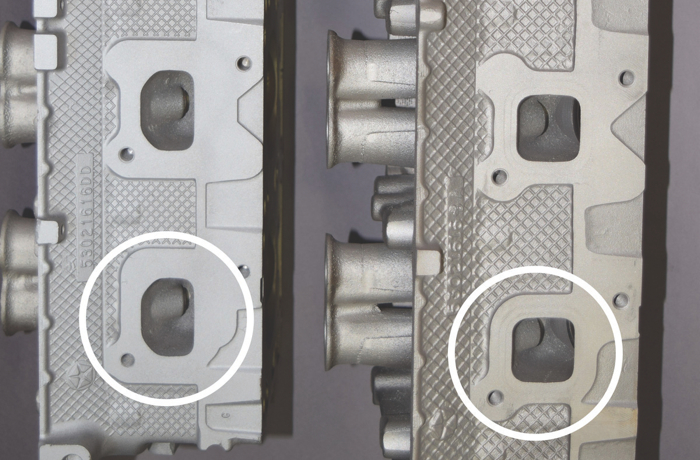
CAM BEARINGS
These engines require a unique bearing set with a wide front bearing that has two slots that are located directly over the grooves in the cam journal and the number three bearing is babbit coated to “reduce friction at a critical point on the cam, which improves durability during cold operation.” Dura-Bond offers a bearing set for these engines.
LIFTERS
All of the VVT cams have more lift, so both the standard and “de-ac” lifters were modified to accommodate the difference. The VVT lifters can be used in the early motors that had the lower lift cams, but the early lifters won’t work in the VVT motors because they can’t accommodate the high lift cams when they are collapsed in the MDS mode.
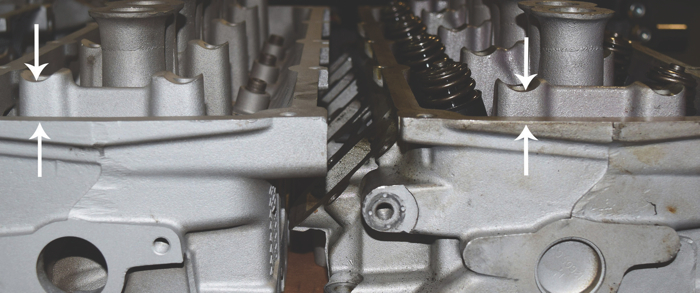
the “Dee-shaped” exhaust ports on the VVT heads. You can see the difference on the one on the left.
The VVT lifters are easy to identify because the flats on both sides are wider and the top is chamfered to make it easier to install them in the plastic yokes.
PUSHRODS
The pedestals for the rocker shafts were raised up by nearly 0.200” because the top of the head casting was moved up to make room for the new “Dee-shaped” exhaust ports, so the pushrods are all about 0.150” longer. That means the valves are longer, too.
CAM PHASER
All of the Hemi motors built since ’09 have a cam phaser that provides variable valve timing “for improved breathing and better volumetric efficiency under a wide variety of conditions.” Using VVT, Chrysler could advance the cam to increase torque under light loads so the engine could run on four cylinders at 70 mph and stay in MDS up to 40% of the time. It also allowed Chrysler to eliminate the EGR valve on everything but the ’09-’10 Aspen and Durango that were built on an existing platform with a PCM that apparently couldn’t accommodate the use of VVT for EGR.
All of the rest of the VVT applications create EGR by retarding the cam to leave some residual exhaust gas in the cylinders. Just for the record, Chrysler built less than 10,000 of the ‘09-’10 Aspen and Durango sport utilities with the VVT engines. Both of them were discontinued on December 19, 2009 and they’re the only ones that had an EGR valve in ‘09-’10, so we’re convinced that it’s an electronics issue and not a mechanical problem.
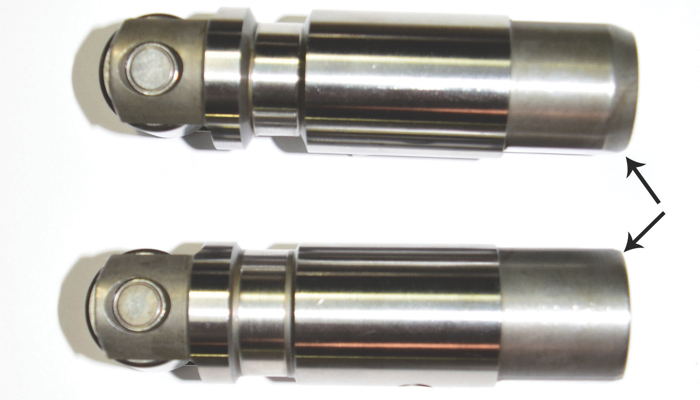
HEADS
The VVT motors came with an all new head that incorporated several notable changes. We suspect that the Hemi chamber didn’t provide enough quench and squish, even with the “squish shelves” on both sides of it, so Chrysler probably had to switch over to an oval chamber to meet emissions.
There are two different casting numbers for the “Eagle” head as it’s known, but both heads are identical with an EGR pad on one end. The only reason there are two different casting numbers is to allow them to differentiate the right from the left on the assembly line when they drill the right head for EGR, and, NO, I’m not making that up. Here’s what’s new and different on the heads:
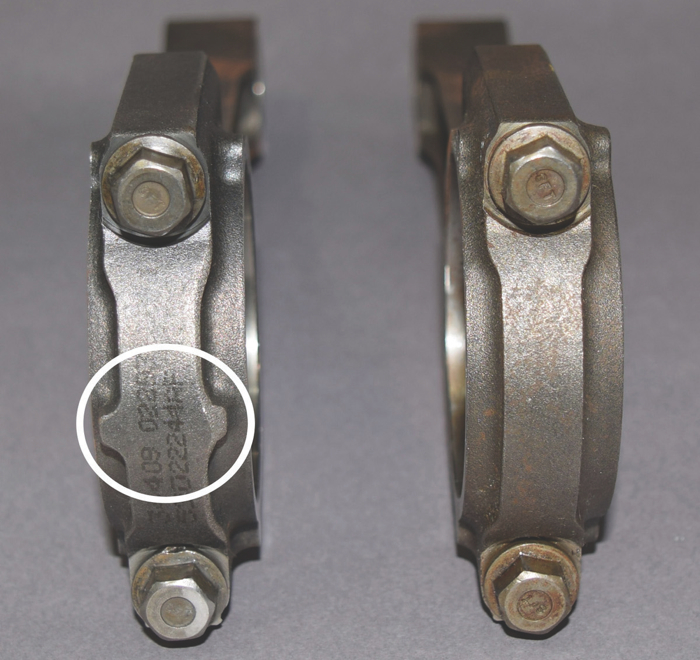
1.
They have a 65cc oval, closed chamber instead of the 85cc hemi chamber that was used for the early heads, so the compression ratio was increased from 9.6:1 to 10.5:1 “to improve the combustion process and therefore efficiency.”
2.
The intake valves are slightly bigger at 2.05” instead of 2.00”, but the exhaust valves are still 1.55” like the early ones. Both valve stems are longer because the rocker pedestals were moved up higher on the head to make room for the new exhaust ports.
3.
The new, square intake ports flow 323 CFM at 0.500” of lift. That’s about 14% more than the ones on the original Gen III heads and they actually flow better than the ones that were used on the 6.1L motors for the SRT, but the SRT heads are still better overall.
4.
The “Dee-shaped” exhaust ports on these heads flow about the same as the square ones on earlier heads, but they’re shaped like the ones on the 6.1L SRT heads now.
5.
The left head is a 53021616DE and the right one is a 53021616DD casting. They both have a pad for the EGR valve on one end, but that only matters if you’re building an engine for the early Aspen or Durango because they’re the only ones that need the two bolt holes and the exhaust passage drilled for EGR on the right head. Otherwise, the heads are interchangeable.
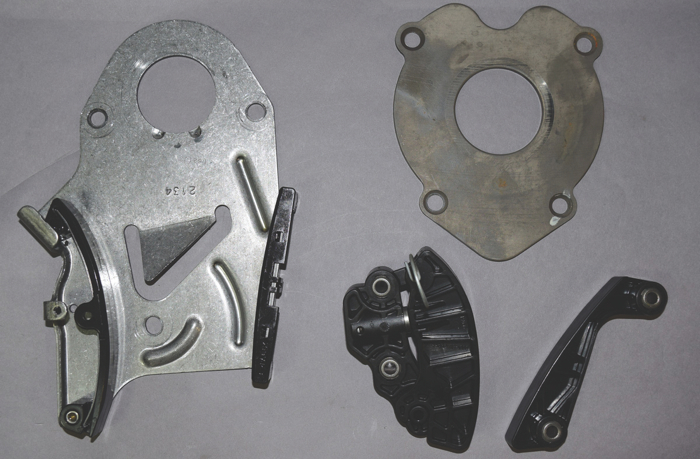
OIL PUMP
The oil pump is still a gerotor design that’s bolted directly to the bulkhead on the front of the block. The original part number 53021622BE was superseded by a ‘BF that was replaced by a ‘BG that was superseded by the current number, which is a 53021622BH. They’re all similar (although there were some internal changes made to the ‘BG and ‘BH), but they’re all high volume pumps that displace 22% more oil than the original Gen III pumps and they’re all interchangeable.
The late, high volume pump, will physically bolt on the early motors, but it was moved out about 0.500” when the front of the block was modified, so the splines on the early crank gear will barely touch the flats in the new pump. I bet that’s why Chrysler says you can’t use the new high volume pump on the original Gen III engines.
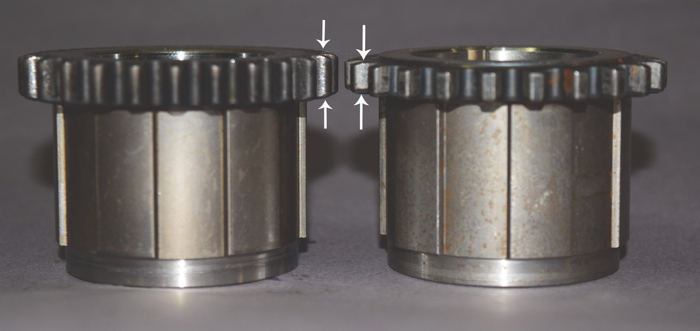
CRANK SENSOR WHEEL
The original Gen III motor came with NGC so it had the 32 tooth crank sensor wheel, but they stepped up to a 58 tooth sensor wheel on the new motor because the computer “needed more immediate and accurate information on the position of the crankshaft during rotation” so it could control and coordinate MDS and VVT along with direct ignition and all of the other electronics used on these engines.
Keep in mind that it deactivates four cylinders in firing order sequence, with the exhaust valve closed, in about 10 milliseconds when the computer commands MDS. That’s less time than it takes the cam to make one revolution at anything much above an idle, so the VVT motors needed a 58 tooth crank sensor wheel along with a 4X cam sensor and a faster PCM.
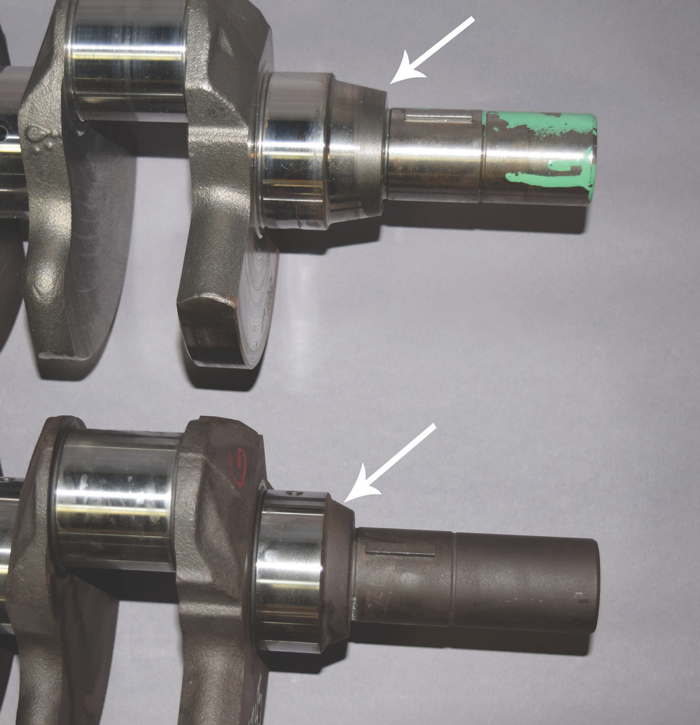
TIMING COMPONENTS
All of the timing components were revised, too, including the gears, the chain, the tensioner and the guide. The cam gear is an integral part of the cam phaser so it’s not available separately.
The crank gear has 23 teeth instead of the 26 found on the old gear because the pitch on the chain – the distance between the links when measured from center-to-center on the pins – is longer, so the new chain has 76 links instead of the 86 links found on the old one and it’s about 0.100” narrower, too.
The colored links on the original chain were replaced by three laser-etched rectangles on the links that are used to time the gears. And, the front cover that included the cam thrust plate along with a blade-style tensioner and a chain guide has been replaced by three pieces including a separate cam thrust plate, a plastic chain guide and a tensioner with a spring-loaded piston.
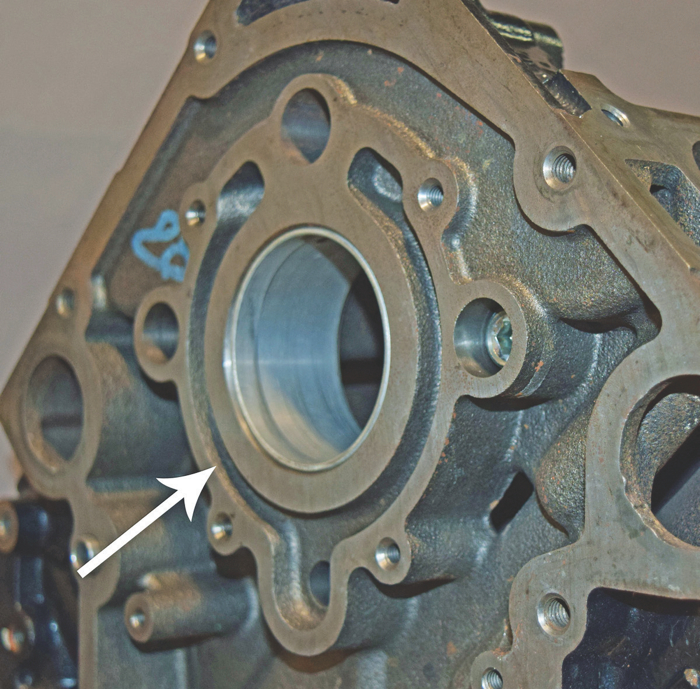
ACTIVE INTAKE
Although the active intake isn’t included with the long block, you will need to know whether the vehicle has one before selling an engine because it requires a special cam to work with the active intake. You can’t depend on the VIN code to identify which engines have it because Chrysler calls them all VIN “T” even though there are five different ones.
Chrysler installed the “active intake manifold” that varied the length of the intake runner “to expand the engine’s torque and horsepower range” on some, but not all, applications. When it’s activated, the butterflies in the intake runners open up at 4,000 rpm to create an intake path that’s half as long, so the engine makes an additional 25 horsepower without losing any torque and ends up with 390 horsepower. You can actually feel the difference when the short runner valve switches over in my pickup truck.
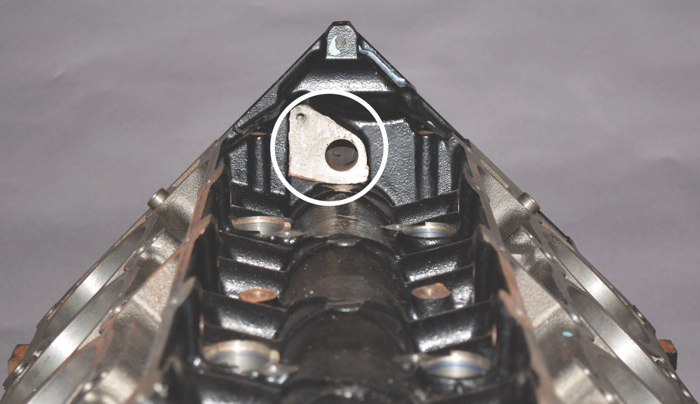
CONCLUSION
When Chrysler updated the Hemi in 2009, they created a state-of-the-art pushrod motor that performs well in all its cars and trucks. The VVT motors all make over 400 lbs. of torque, and the pickups with the active intake are rated at an honest 390 horsepower. They deliver reasonable fuel economy in every application and they’ve been virtually trouble-free since they were introduced in 2009.
My crew cab pickup has pulled a 5,000-pound car trailer down the road at 75 mph without a complaint and it delivered 18.2 mpg on a 2,600 mile road trip to and from Minnesota last summer, so I’m a believer.
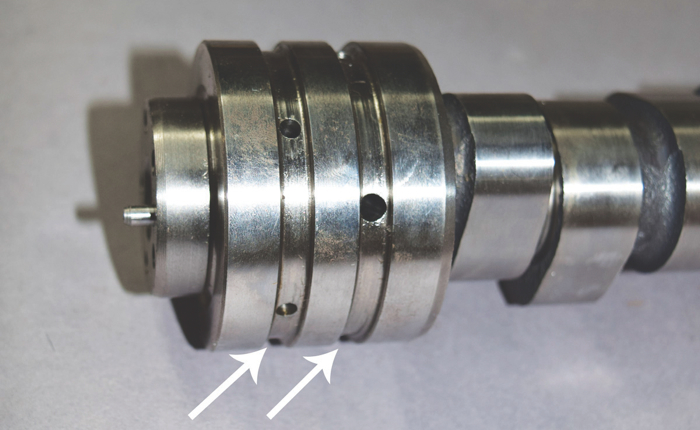
Chrysler has been selling around 400,000 trucks a year for some time now, so that means there are a lot of these Hemi motors out there that will end up getting rebuilt sooner or later because the trucks will be worth fixing when they need an engine. Just make sure you figure out which one fits the application before you send it out the door.
Doug Anderson is Manager of Technical Services for Grooms Engines, located in Nashville, TN. He has authored numerous technical articles on engine rebuilding for Engine Builder magazine for more than 25 years. Anderson has also made many technical presentations on engine building at AERA and PERA conventions and seminars.